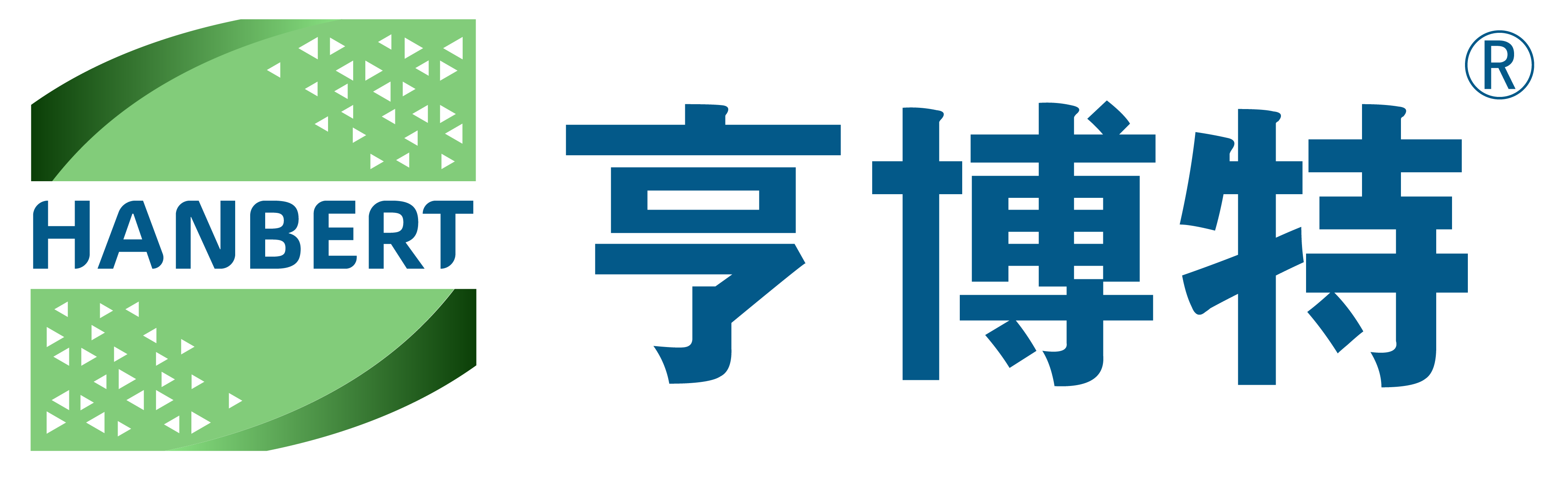
The project is located in Xi'an with a rich historical and cultural heritage. During the Chang'an period, there was a very advanced concept of "Lifang System" construction, which pursued the orderliness, modularity, and grid transportation of the city. This project also pursues orderliness and modularity in the overall layout.
The children's hospital building adopts the design concept of "LEGO" splicing, which has a childlike charm while continuing the modular design concept of the building.
The logo of a children's hospital is a four color block, which is derived from the building volume to form a four color block for the exterior curtain wall of the building.
From the facade, the entire building has a relatively regular exterior without too many complex components.
The highlight of the project's exterior design lies in the variable angle dual color grille on the exterior facade. The architectural concept of the project is to pursue people's viewing of the building from different perspectives, which can bring different color sensory experiences to people. The grid size is 500mmx80mm, with a total length of 32000m and a height of 3100mm. The grid colors are selected in combination with green, yellow, red, and purple.
Mechanical application design concept: top and bottom connection hidden design
Difficulties and key points in designing dual color gradient angle grilles:
1、How to achieve a 500mmx80mm ultra large rectangular grille section?
2、How to achieve diagonal color matching?
3、How to achieve grid angle change?
How to achieve prefabricated installation with top and bottom connection design? And implement hidden design? 4. 5. Installation difficulty: How to avoid handing over homework? Improve installation efficiency.
6、How to ensure the overall effect of the grille while completing the above design?
We have considered the refinement of architectural details and adopted a profile scheme. Considering the economy and processing cycle of dual color spraying, we have adopted a split scheme to ensure the final processing efficiency.
We have designed multiple schemes for comparison:
1、Overall plan
The extrusion thickness of the profile should be at least 6mm or more. Double color spraying requires secondary furnace feeding, making it difficult to ensure the yield of processed products.
2、Split scheme
The profile undergoes routine treatment with two slits in the middle, which greatly damages the overall effect. The economy of dual color spraying still exists.
3、Diagonal Splitting Scheme
The difficulty of profile extrusion is high, making it difficult to achieve hidden connections.
4、Profile manufacturer's plan
A good consideration is given to the economy of the profile and the thickness of the extrusion, but there are too many components with joints, making it difficult to control angle changes, resulting in poor economy and poor effectiveness.
5、Final diagonal split scheme
Make two splits from the color transition position of the feet, visually weakening the splits through color gradients. The profile is L-shaped with flying wings, which minimizes the thickness of the profile. Two profiles are interlocked to form three cavities, ensuring overall strength and stability. The middle grille insert connects the two profiles more firmly.
The top and bottom of the grille have an outward convex aluminum plate shape, which minimizes disturbance to the aluminum plate system and avoids functional damage to the aluminum plate, such as water leakage. We consider integrating the grille and upper and lower aluminum panels as closely as possible to ensure the overall effect.
From a construction perspective, a welding free design, convenient installation and positioning, and lateral "rotating installation" are adopted to meet the requirements of adjustment (temperature expansion height adjustment) and hidden design.
The connection system at the bottom draws inspiration from the connection method and adjustment principle of claw components, and locks and adjusts the height direction at the bottom through sleeves and threads.
The bottom connected split is first connected to the trapezoidal connector at the bottom and the keel of the aluminum plate. The connection is ensured by inserting the bottom support and the top grille core, and the angle is rotated.
The bottom support member and the pillar are connected and adjusted in height direction through threads, and finally locked and positioned with self-locking and anti torsion components. Insert two small cavities in the middle of the anti torsion component to avoid rotational deformation.
The top connecting components refer to the insertion method of connecting the horizontal and vertical bars of the railing, including the line position for nailing. The connection between the top and bottom takes into account the installation space.
At the top, a U-shaped adapter with grooves is used, and the middle groove reserves space for the connection of the entire grille, minimizing the gap between the grille installation and the top aluminum plate.
The two split semi-circular adapters in the middle can be connected on both sides after the installation of the grille. The split and the top groove adapter can be pre connected and positioned through long bar holes. In addition, 10 fiber holes were made according to the variable angle, corresponding to different angles of the grille, and the angle was automatically matched between the positioning holes of the circular adapter.
We conducted secondary research and development based on LISP programming to address the issue of variable angle grid layout. We developed a CAD parametric plugin that can achieve rapid layout of variable angle grids, solving the problem of angle adjustment and layout, and improving the production efficiency of design and construction.
In terms of layout technology, the development of dimension annotation modules, including automatic width adjustment and automatic placement of embedded parts, greatly improved the design efficiency of the project.
数字化应用思路
模块化只是手段,数字化才是目的。只有数字化才能契合现在行业的人工智能及参数化的应用。
数字化应用思路:程序的模块简化一特征归纳一程序的深度学习一数字化处理。
We envision achieving the ultimate goal of wall design through architectural structural design, combined with program modules.
Components and Installation
Quick installation in minutes
Innovation in installation methods: reducing cross operations and improving installation efficiency; Automatic locking angle; Prefabricated installation, easy and fast to install.
Firstly, the installation of the bottom and top components is carried out, and the top is fixed with nails. The entire installation process of the grille takes about a few minutes, greatly improving the efficiency of the grille installation.