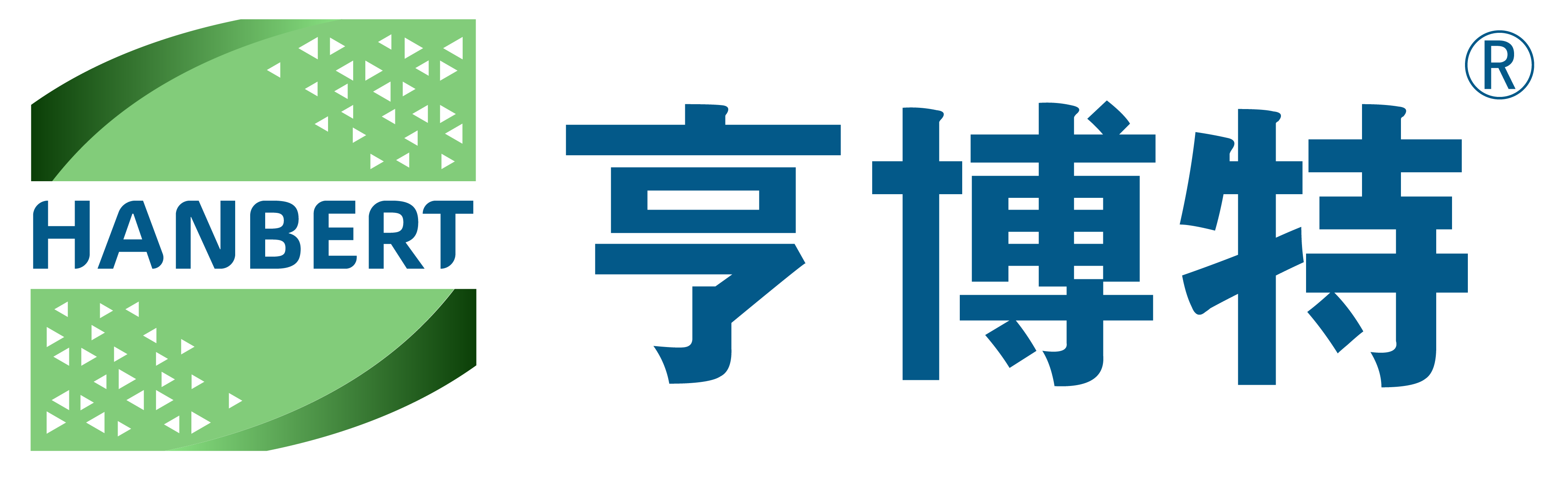
There are mainly two types of aluminum panels for exterior wall decoration: spray coated aluminum panels and roll coated aluminum panels. Spray coated aluminum plates are first processed into aluminum veneers through sheet metal technology, and then coated with fluorocarbon paint on the surface. Roll coated aluminum plates are then coated with fluorocarbon coating on the surface of the aluminum plate through roll coating technology and processed into shape through sheet metal processing. So, which is better, spray coated aluminum plates or roll coated aluminum plates? Why are spray coated aluminum plates more commonly used in exterior curtain walls, while roll coated aluminum plates are used less frequently?
In fact, the advantages and disadvantages of spray coated aluminum plates and roll coated aluminum plates have been introduced in detail before. Spray coating is suitable for complex shaped aluminum veneer products and is often used for customized processing; Roller coating is suitable for large-scale standardized production of aluminum plate coating. The reason for the topic that appears at the beginning of the article is that aluminum plates are prone to cracking when bent, which is determined by the material properties!
Aluminum sheet metal bending can cause cracks, mainly due to the following reasons: ① The hardness of the aluminum plate is too high, which can easily lead to cracking during bending. ② Thick aluminum plates are prone to cracking when bent The smaller the bending R-angle, the easier it is to crack The bending direction is parallel to the texture direction of the aluminum plate, and the probability of cracking is higher.
Spraying aluminum plates, due to the process of sheet metal first and then spraying, can effectively conceal this problem and reduce the damage to curtain walls caused by cracks. However, roller coated aluminum plates do not have such conditions. Only by selecting appropriate coatings and aluminum materials, as well as taking appropriate measures during the bending process, can the problems of cracks and paint film fracture and detachment of roller coated aluminum plates be effectively reduced during bending. I have summarized the following methods for reference only:
A. Choose high-quality coatings to ensure good adhesion and appropriate hardness;
B.Generally, aluminum veneer manufacturers will choose aluminum materials of 1100H24 and 3003H24. The former is pure aluminum, while the latter is aluminum manganese alloy with moderate strength, suitable for sheet metal bending processing;
C.During design and production, pay attention to adjusting the size of the bending R angle to ensure the appropriate size to reduce the possibility of cracks and fractures;
D.The bending direction should be perpendicular to the texture direction of the aluminum plate, avoiding parallelism to reduce stress concentration and minimize the occurrence of cracks.