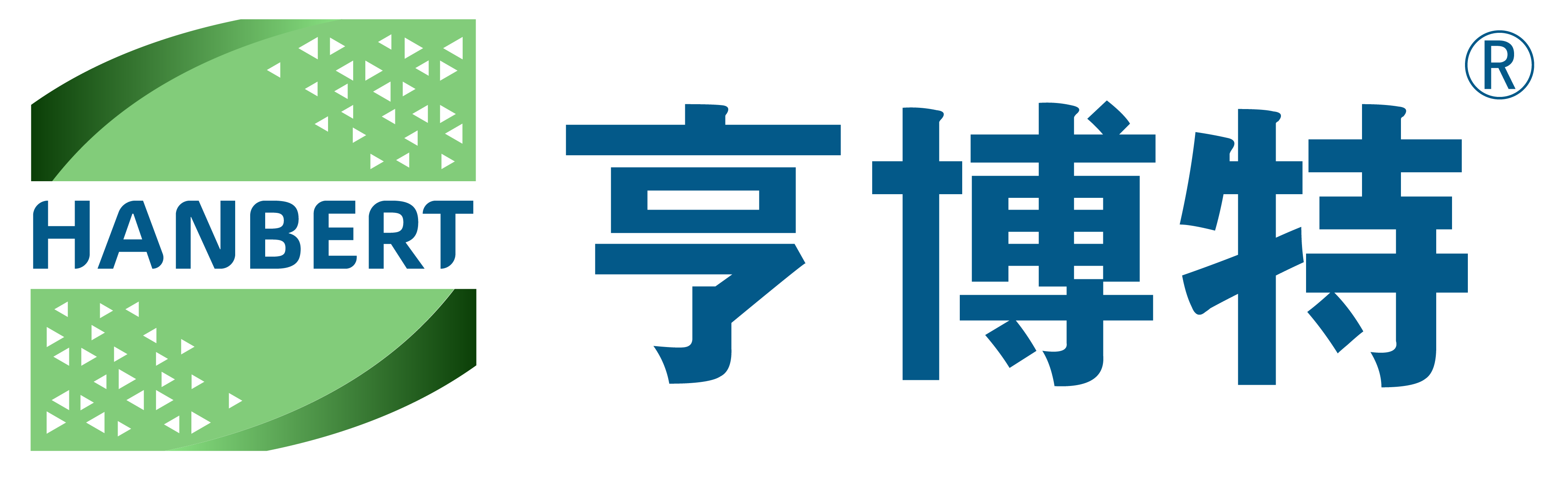
Metal aluminum plates themselves only have one color, but various treatments can be applied to their surfaces. Through processes such as spray painting, coating, wood grain application, and cloth patterning, a rich and diverse range of colors can be achieved on the surface of the aluminum plate.
Fluorocarbon paint is highly regarded in the architectural decoration industry due to its wide range of color options, excellent weather resistance, and corrosion resistance. With the rapid development of coating technology, the superior performance of fluorocarbon coatings has made them increasingly widely used in architectural decoration materials.
Today, we will delve into the differences between fluorocarbon spray coating and fluorocarbon roller coating processes, and explore which type of aluminum panel material is suitable for each application.
01.Process Definition
Fluorocarbon spraying process operation diagram source network
Fluorocarbon spraying
Fluorocarbon spraying is an electrostatic spraying and liquid spraying method. It refers to the coating method that uses the principle of corona discharge to make atomized coatings negatively charged under the action of a high-voltage direct current electric field, and adsorb onto the surface of a positively charged substrate for discharge.
For example, the common aluminum veneer is first processed and formed according to the drawing, then polished clean, sent to a cleaning tank for alkali washing and acid washing, and then sent to a spray paint room for spraying and baking, forming a spray layer on the surface to isolate the external air and pollutants from directly corroding the substrate.
The fluorocarbon spraying process mainly consists of three steps: pre-treatment (degreasing, acid washing, chroming), spraying, and curing (baking). According to the requirements for material coating, two coats, three coats, or four coats can be selected. Second coat (primer+topcoat); Three coats (primer+topcoat+topcoat); Four coats (base coat+barrier coat+topcoat+topcoat). In general, the average thickness of the second coat coating is ≥ 30um, and the average thickness of the third coat coating is ≥ 40um.
Fluorocarbon roll coating
Fluorocarbon Roll Coating Process Flow Diagram Source Network
Fluorocarbon roller coating is a coating method that uses rubber rollers or steel rollers to apply paint to the surface of an aluminum plate, allowing the coating to flow and arrange, and finally evenly transfer it to a moving metal sheet (steel plate or aluminum plate) for baking and curing, thereby forming an organic solid protective film on the metal sheet.
Fluorocarbon roller coating is commonly used for surface treatment of metal sheet substrates, also known as pre coating. For example, the common aluminum composite board is usually produced by placing the coil on the production line for surface treatment, then rolling it with fluorocarbon paint and baking it to form the product. The rolled coil usually requires secondary processing and molding before use.
The production process of fluorocarbon roller coating is to apply and bake at the same time, usually several times of coating and baking are required. The commonly used ones are three coats and three baked or two coats and two baked. In general, the average thickness of a two coat and two bake coating is>25um, and the average thickness of a three coat and three bake coating is>32um.
02.Process Distinction
Harwyn Pod © Harwyn
The difference between fluorocarbon spraying and fluorocarbon roller coating processes is not only in their surface effects, but also in the sequence of aluminum plate film-forming and forming processes.
Spray coated aluminum plates are first processed into sheet metal shapes, which can be folded, carved, bent, connected, punched, etc. The shape is convenient, the plasticity is strong, and it will not have any impact on its surface. Fluorocarbon roller coating requires the thin aluminum coil to form a film first, which means that many processes need to be restricted to avoid damage to the paint surface, and it is difficult to unify the color during later repair.
Advantages of Fluorocarbon Spray Coating Process
1).The spraying process is carried out after the aluminum plate is formed. Small defects in the aluminum plate itself and newly added defects during the forming process can be compensated for through the spraying process, which has considerable flexibility;
2).The spraying construction technology is mature, and the coating performance is good. The film thickness can reach 50-80um, and it has excellent comprehensive indicators such as adhesion and corrosion resistance;
3).There are various colors available, and various colors can be made according to customer requirements, but the color scheme is relatively flat.
Roller coating process, illusionary color series © Harwyn
Advantages of Fluorocarbon Roll Coating Process
1).High speed automated operation, fast speed, high production efficiency, no paint mist, no paint mist splashing.
2).Roller coating is applied due to the pressure on the flat plate, resulting in uniform force on the surface and a paint film thickness error of less than 0.5 microns. The thickness of the entire paint film layer is uniform and consistent, with minimal error. The surface is smooth and delicate, without micropores or pollution.
3).The paint utilization rate reaches over 99%, making it an efficient, energy-saving, and environmentally friendly product with low loss.
4).Roller coating can print various patterns, including precious wood grain, marble pattern, iridescence and other special colors, and the types of colors sprayed are relatively flat.
In addition, due to the directional nature of the roller coating process, the surface color may appear different under the refraction of sunlight. Therefore, it is important to maintain consistency in a certain direction during installation.
Ensure that the roller coating direction remains consistent during installation © Evaldas Lasya
The fluorocarbon roll coating process has shown significant advantages in production efficiency, coating quality, full lifecycle cost-effectiveness, and environmental impact, while the fluorocarbon spray coating process is an effective choice in certain specific application scenarios, such as handling complex shaped aluminum plates.
Therefore, when choosing a coating process, the most suitable process type should be selected based on specific project requirements, budget constraints, and environmental requirements.